Meter Management System (MMS™)
MMS™ provides accurate meter history and enables process management, saving time and money. It is designed to integrate with our Sonicnine™ Sonic Nozzle Provers and is the preferred meter shop software of many of our customers.
Meter Management System (MMS)
Our MMS™ is a set of software modules that allows you to manage the information throughout your meter shop. Using barcodes to track meters from the time they arrive at your door, through repair, into inventory and back out into the field. MMS™ collects data from provers and other shop stations and has standard and custom reporting.
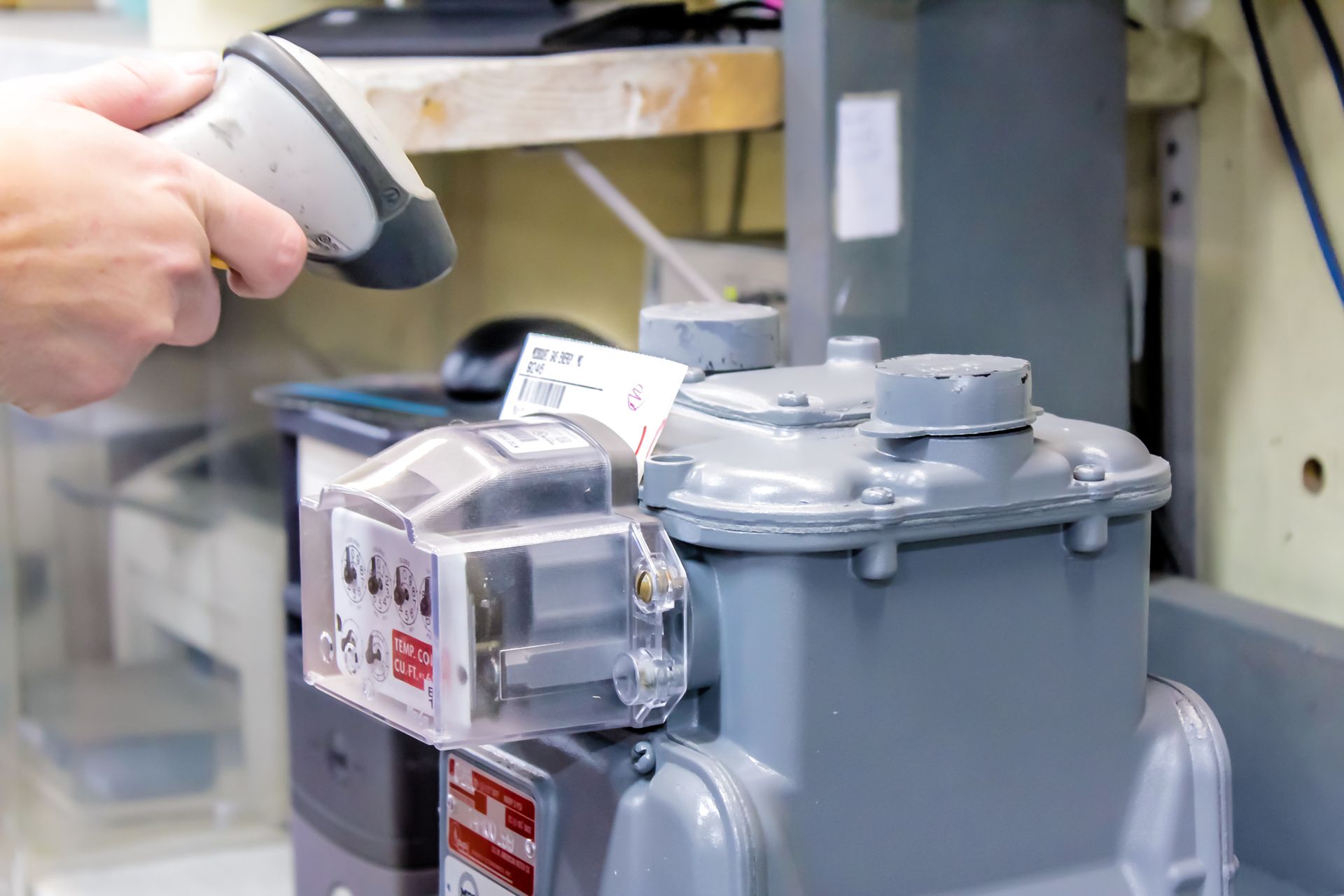
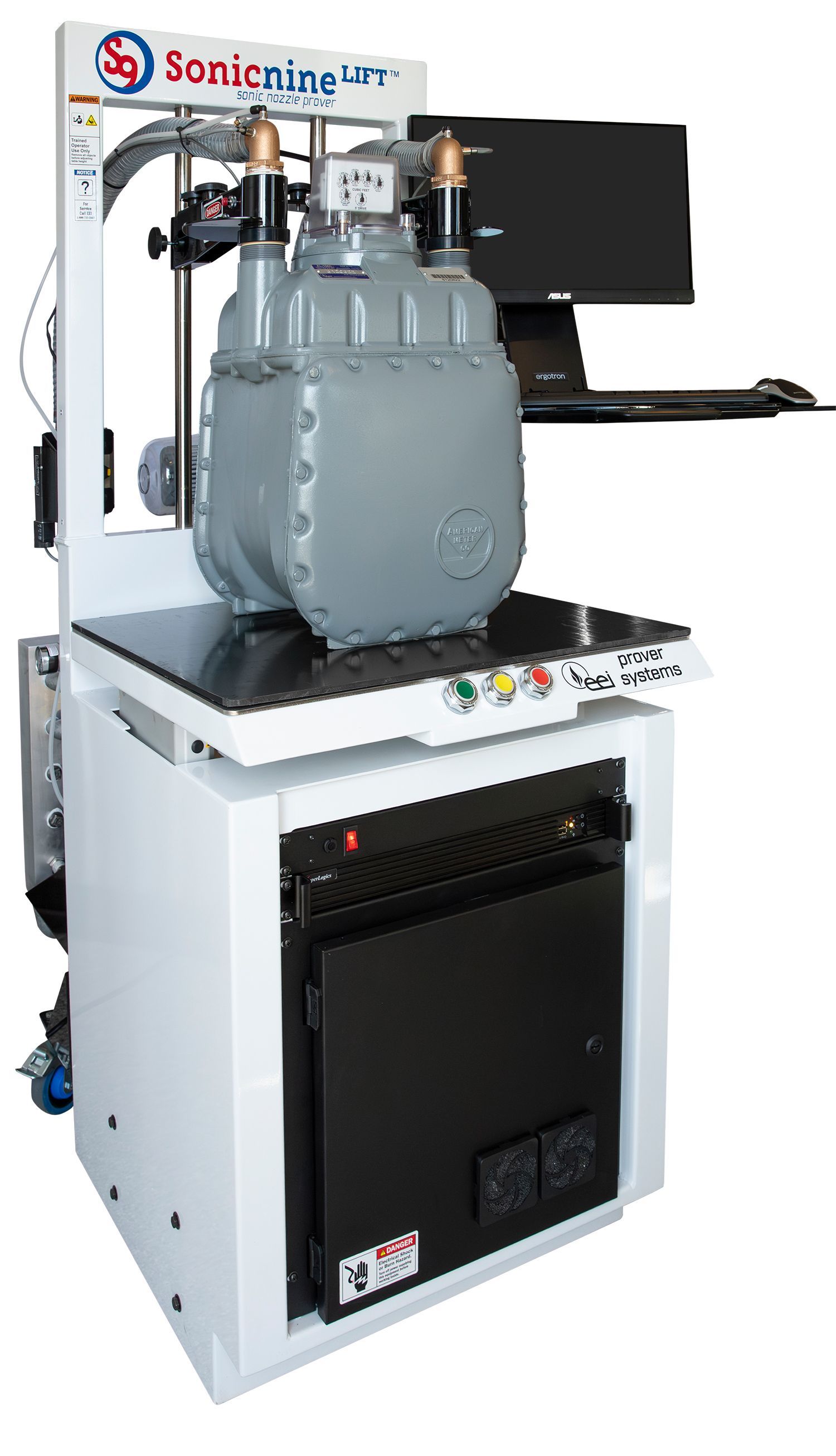
Principle Functions
- Collects meter test results from a variety of leading manufacturer’s proving equipment.
- EEI Sonic9™ Prover
- EEI Sonic Nozzle Prover
- Weco 2350 Test Board
- Watt-Net Express based Test Boards
- Automatically acquires the test results, limit checks these tests, records test times and dates, and stores histories of any special handling or repairs.
- Tracks meter production throughout the meter shop.
- Locates meter by warehouse, production process and pallet.
- Fail-soft support with EEI provers.
- Supported Client OS: Windows 7/10.
- Provides multiple levels of system security password access from read-only operator to system administrator. Key system parameters, system menus, validation limits, etc. may be set by the appropriate level of personnel.
- Designed for Oracle RDMS.
- Provides standard reports for screens or printers on meter production as well as ad hoc reporting and querying capabilities. Various analysis and reporting functions can be initiated by Windows-based point and click report generating software. Typical reports include:
- Meter accuracy by type, manufacturer, in service dates, etc.
- Productivity reports by operator, test device, meter type, day/week/month
- Reports and data files can be printed or exported to other standard software packages for further analysis or integration.
- Interfaces to customer information systems and work tracking systems.
- Bar-code support is available for reading and printing of labels.
Benefits of MMS
Energy Economics, Inc. has designed MMS™, a multiple user Data Acquisition System, to collect and report the information needed to manage a gas meter shop. While every gas utility has the same responsibility to test and assure the accuracy of its gas meters, each company has slightly different procedures for doing this work. MMS™ has been installed at many gas utilities and each installation implements system features to accommodate the customers’ individual needs, often without custom code. We are dedicated to providing an IT system that manages the information needed in the meter shop.
Collecting data from provers and printing the results is as simple as MMS™ gets. Most MMS™ users find it useful to collect meter information throughout the meter shop and produce specific reports on productivity and meter location. Collecting, storing and reporting information is a task for a database. Client workstations have function specific software such as Receive, Test, Repair, and Stock stations. MMS™ can provide tracking information down to the pallet by reporting where a meter was last processed (check-in, intest provers, repair bench, leak test, out-test provers, check-out, etc.) Other reports provide information about shop production by meter type, prover operator, repair operator or any other criteria desired.
The MMS™ database may be started from scratch or it may be loaded with legacy data. MMS™ can be used as a stand-alone system or communicate with other systems. Our interface design allows easy connections with minimal customization.
The basic objective of MMS™ is to automate the collection of information as a meter is processed by the meter shop. Other important benefits include up to the minute information availability, data integrity, productivity reports and meter tracking, random sampling, periodic testing, inventory reconciliation.
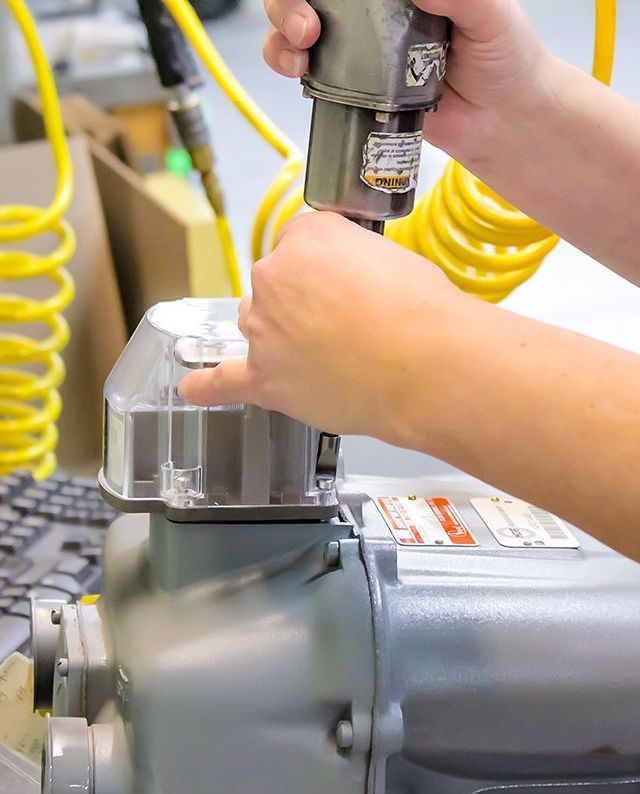